宮崎県西都市にあるデサントアパレル株式会社西都工場にやってきました。こちらの工場では世界で戦うトップスイマーが愛用する「アリーナ」ブランドのスイムウェアの縫製を担っています。
普段はなかなか表に出てこない「アリーナ」の商品ができるまでを追いかけ、工場で働く職人さんたちにお話を伺いました。
※本記事は2019年10月28日に取材しております。(ライター|宮浦 晋哉、カメラマン|村本 万太郎)
「服ができるまで」の背景。どんな工場で、どんな職人さんが働いていて、果たしてどのくらいの工程があるのでしょうか。
現在、国内の市場に流通する衣料品全体のなかで、国内で縫製されたものは全体数量の約3%と言われています。今や、日本国内の店頭に並ぶ商品の多くは海外縫製のものとなりました。
人件費の安い海外で縫製したほうが、より安価な商品を世に出すことができます。一方で、日本製の商品は日本国内で縫製しないとならない意味があります。
西都工場でも、ここでしかできない確かな生産技術があるからこそ、「アリーナ」のトップスイマー向けのスイムウェアを作り続けてきました。
西都工場の軌跡
工場の設立は1973年にさかのぼります。創業当時は現在のメイン商品である薄手商品でなく、ジャージやスキーウェアを縫っていました。
日本の縫製業が海外に移転し始めた1980年代中旬、西都工場はより国内生産の価値を高め、海外生産との差別化を図ろうと、今の工場の特徴でもある「立ちミシン」を導入しました。
従来の縫製工場の生産方法は大量生産型で、1人が1パーツ(1ヶ所)を担当する「ライン式」と言われるものでした。この場合、商品は1枚ずつ完成するのではなく一度に大量に完成します。
そんな「ライン式」に対して、立ちミシンは読んで字のごとく、縫製職人さんが複数のミシンを立ち回り、次々と縫い進めていきます。
大量にまとめて縫い上げるのではなく、1着1着が順々に仕上がっていくので、その都度の検品が可能になり、改善点があればリアルタイムで縫製職人さんにフィードバックを出せるようになりました。量より質を追いかける考え方から生まれた方式です。
また、間髪入れずに1着を縫い進めるので、リードタイムの短縮にもつながります。少量、中量の生産にとても効果的な生産方法です。これにより短納期のニーズにも応えられるようになりました。
接着縫製技術の導入
そして10年前、トップスイマー向けの競技水着の縫製のために、西都工場は新たに接着縫製用の機械を導入しました。
初めて取り組んだ接着による縫製加工で、導入直後はなかなか品質が安定しなかったそうです。何度も何度も失敗して、試行錯誤を繰り返しながら、接着縫製のノウハウを蓄積していきました。
「アリーナ」のスイムウェアの縫製はこの接着縫製が要です。極力、水の抵抗を減らすために、トップアスリートのスイムウェアには、薄く伸縮性のある生地と接着縫製の技術が不可欠となっているのです。
接着縫製というのは、アイロンを使って手作業でパーツに専用の接着テープを仮止めする作業と、10年前に導入したローラープレスという機械を使って、熱で接着剤を溶かしながら圧力を加えてパーツとパーツを接着していく作業です。
通常の縫製よりはるかに手間がかかり、技術も要します。
「接着縫製は、少しでも失敗すると途中でやり直しができません。一発勝負なんです。着々と作ってきても最後の1工程で失敗してしまったら不良品となってしまうんです。非常に緊張感があり高い技術力が求められる縫製です。」と接着縫製の難しさを説明してくださったのは、工場全体の生産管理をする生産課長の島田さん。
「アリーナ」競泳用トップのスイムウェア用の生地はとにかく薄く、そしてはっ水性のあることが特徴。そのはっ水性のある生地と接着剤とがなじみづらく、だからといって接着の圧力を増やせば繊細な生地にダメージが出てしまう。
競技水泳に耐え得る高い強度を保ち、安定生産まで持っていくのが非常に難しかったと開発時期の頃を振り返ります。
蓄積してきたノウハウがあり、多くの技術者がそろうデサントの西都工場だからこそ成り立っているモノづくりと言えます。
西都工場だからこその強み
現在、西都工場には110人の職人さんたちが働いていて、年間約20万点、1000品番以上の商品を縫っています。そのすべてが立ちミシンです。
大量生産する工場でなく、他社ではなかなかできないような難易度の高い商品を少量作る工場です。
縫製工場では、通常同じアイテムを数週間縫い続けるということも珍しくないですが、西都工場では1日のうちで異なるアイテムを3種類縫うこともあると言います。
こういう環境が、職人さんたちの高い技術力の蓄積につながってきました。
勤続30年以上となるベテラン縫製職人の江藤さんに、西都工場の強みをお尋ねして最初に出てきた言葉が「品質も維持しながら、とにかく納期を守ること」。そのために縫製チーム内での確認、連携が何より大切と言います。
一つひとつの丁寧な積み重ねが社内外での信頼関係を築き、品質と技術を高めながら歩んできた、まさに西都工場の今の姿を表す言葉です。
職人さんたちが立ってミシンを動かしている姿、多種多様な機械がズラーッと並んでいる様子、働く職人さんたちの手の早さ、工場内の圧巻の光景を次々にご案内いただいた終盤にもう一つ驚きました。
それは、衣服を生産する縫製工場の中に、まるで金属加工場のような製造スペースが出てきたことです。
立ちミシン導入と同じく1985年に、社内で機械品や部品の加工と修理、製造をできるようにと作られました。
工場内でミシンの改造、修理も逐一できる状況にあることが、縫製職人さんたちの仕事の質を保つことにもつながっています。心強いことに、機械保全専属の社員さんが4名もいらっしゃいます。
「国内自社工場だからこそ、その時代のニーズへの対応力を高めていかないとならない。10年前に接着用の設備を自社に取り入れたように、今後もその時代のニーズを聞きながら、他社では難しい技術も積極的に取り入れていかないとならないと思っています。」と話すのは、工場の改革を経験してきた、塩月工場長。
日々開発される新しい生地や形、縫製など服のつくりもどんどん新しくなるので、そこに対して縫製技術も適応しながらデサント商品の高い品質を保つことが難しいところですが、プレッシャーであり誇りでもあると語ります。
そんな西都工場でだからこそ成せるモノづくりを象徴するアリーナのアイテムが「アルティメット・アクアフォース エックス」という名の付いた2つの新モデル。
満を持してアリーナからリリースされたこだわり抜いたスイムウェアです。
1つ目のモデルは、軽量と動かしやすさを追求した「アルティメット・アクアフォース エックス.MF(MOTION FREE)」。その名の通り、採用した軽量素材、切り替えのない仕様から、スイマーの動きがより自由にするよう開発されました。
使われている素材は0.2mmの薄さで、1m×1mの重さがわずか88gとのこと。通常モデルより生産の難易度の高いこのモデルは西都工場で1日最大90枚の生産量です。この商品1着ができあがるまでに50以上もの工程があるとのことです。
2つ目のモデルは、水中でのボディポジションをコントロールしてくれる「アルティメット・アクアフォース エックス.CP(CONTROL POSITION)」。
なんとこちらは1日最大60枚しか生産できず、工程数は70を超えると言います。
先ほどご説明した接着技術により、お尻の部分からハムストリングまで専用のグリップテープが貼られていて、スイマーとウェアのズレを軽減して身体にフィットしてくれます。
「アルティメット・アクアフォース エックス」はトップスイマーのことを考え、改良に改良を重ねてきました。
激しい動きに耐えつつもパフォーマンスを助ける厳選された素材、メンズ・レディースそれぞれの身体の曲線に沿うよう考え尽くされたパーツの形と数、水中での抵抗を減らす接着縫製、果てしない工程数、それらを支える西都工場の職人さんたちのモノづくりへの追求。
「アルティメット・アクアフォース エックス」は、妥協のない「アリーナ」ブランドと西都工場の技術が集結して初めて生まれた商品なんです。
アルティメット・アクアフォース エックスはこちら!!
アルティメット・アクアフォース エックス.MF(MOTION FREE)
アルティメット・アクアフォース エックス.CP(CONTROL POSITION)
15年もの長い間、日本代表として世界と戦い続けている入江陵介選手(イトマン東進)。今年の4月に行われた第97回日本選手権水泳競技大会 競泳競技でも、50m、100m、200m背泳ぎで3冠を達成しました。100m背泳ぎでは8年連続10回目の[…]
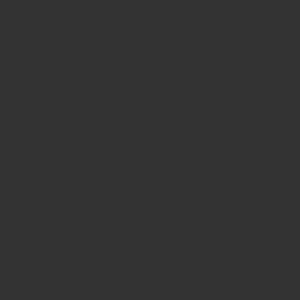